oneLab equipment status
Equipment status use
In oneLab, the equipment status is used to indicate the actual state an equipment (or module) is currently in. Having up-to-date information on equipment status results in:
Efficient communication and information sharing
Is the equipment available for use?
Who should take action on the equipment?
What is currently happening on the equipment?
Reporting and improvement actions
Equipment with recurring bad performance KPI’s requires appropriate actions (preventive/corrective maintenance, calibration, ...)
This reporting is important to define and prioritize supplier actions and potential investments (tool upgrades, spare part kits, ...)
Changing an equipment status
It is the responsibility of every user of a tool to ensure that the oneLab tool status correctly reflects actual status of this tool. To this end, everyone is required to check the equipment status in oneLab prior to using or performing another action on the equipment and change the equipment status in case this should not be correct.
Where to find the equipment status?
The current status of an equipment in oneLab is always indicated next to the equipment name (including a color code of the status):
In equipment overview lists: left of the equipment name, in the column “Status”:
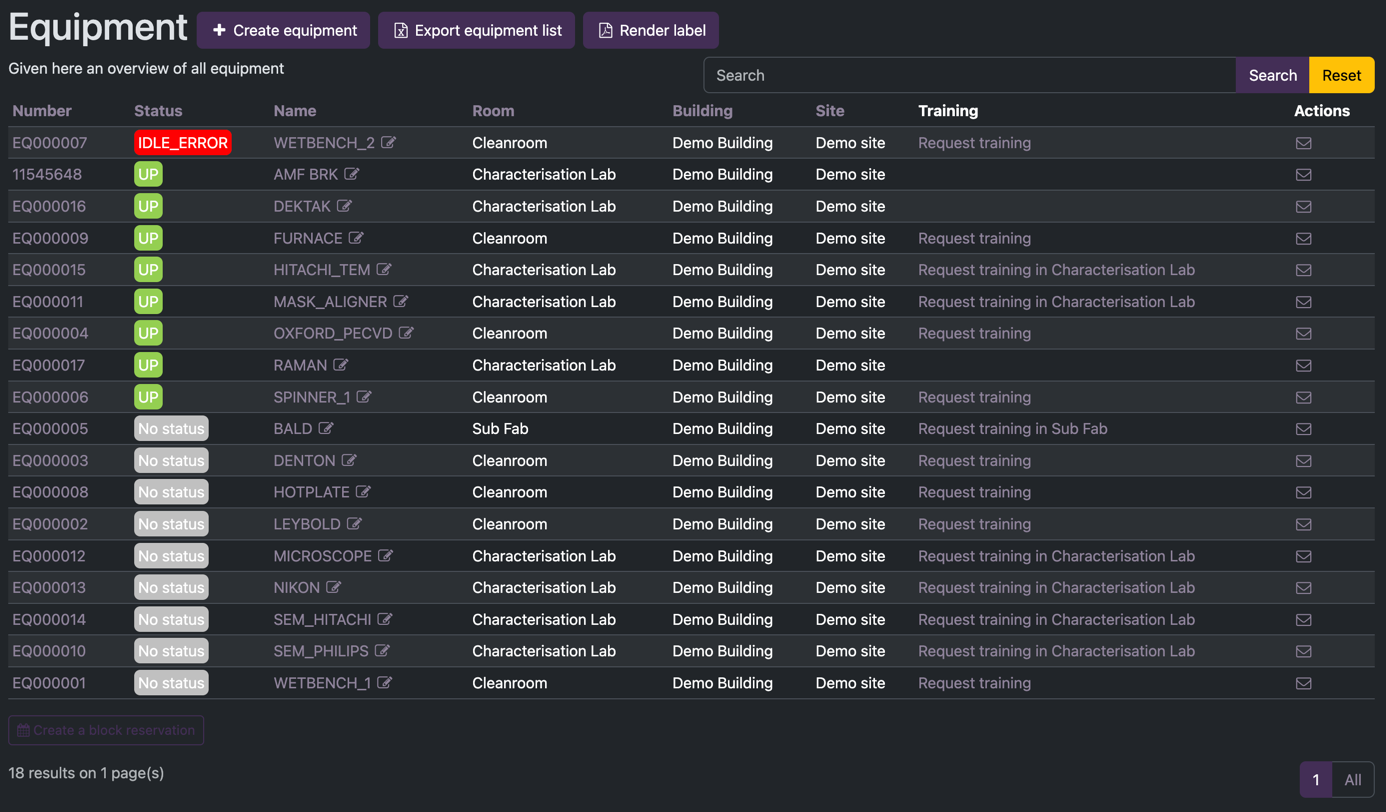
On the dedicated equipment page: right of the equipment name:
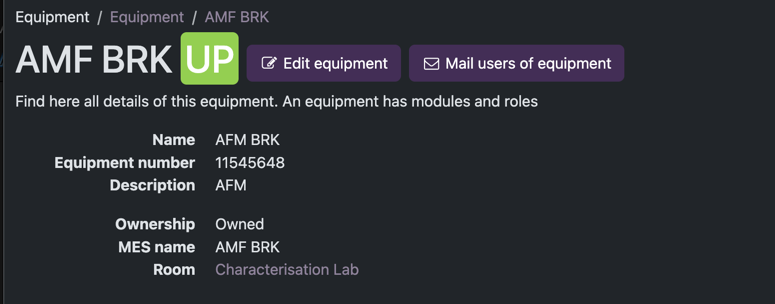
How to change the equipment status?
The colored status button next to the equipment name is a clickable button, that opens a “Update status” popup window:
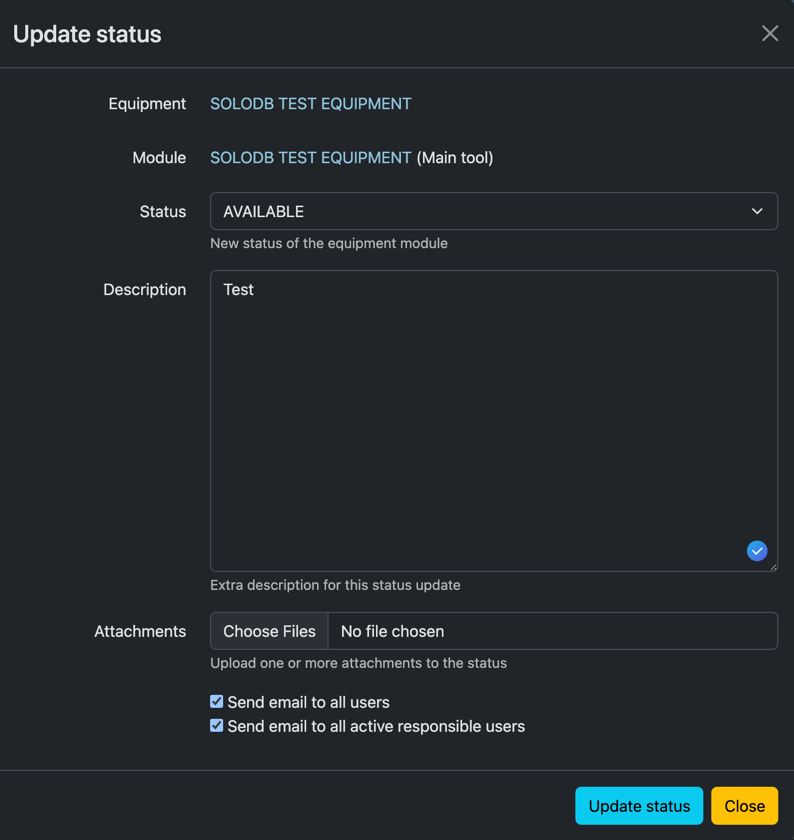
In this popup window, the following actions are available:
Description: free text field, to be used to share information on the reason for changing the equipment status (e.g. description of an error occurred during use, causing the tool to be put in status IDLE_ERROR). As a starting point, this will contain the last description entered when a previous status update was performed.
Status: dropdown menu to select a new equipment status.
Attachments: offers the possibility to add files such that more relevant information can be shared (e.g. screenshot of an error code)
Send email: checkbox which can be selected to automatically send an email notification to either all users or the equipment’s active responsible users. This email will be sent when updating the status.
Update status: confirm your entries and update the equipment status using the button “Update status”.
Important note: in case of an equipment containing multiple modules: when applicable, please update the status of the module(s) affected, not the main equipment.
Equipment status definitions
Below is a list of all equipment statuses available in oneLab. Please ensure the equipment always has the correct status selected, based on the definitions provided:
UP: The equipment is performing its intended function (productive + idle status)
PARTLY_UP: Part of the equipment or available processes is performing its intended function, other part is experiencing downtime.
SPC_TEST: Planned interruption of equipment availability for evaluation of performance (SPC test)
SET_UP: Ongoing equipment installation/rebuild/upgrade/...
MAINTENANCE: Scheduled downtime: (preventive) maintenance, test, consumable change
IDLE_ERROR: Unscheduled downtime; analysis of problem needs to start
IN_REPAIR: Unscheduled downtime; analysis of problem has started (diagnosis, corrective actions, repair delay... * ongoing)
AVAILABLE: Not an equipment status! Only to be used for consumables etc.. managed in oneLab
Note: most of the equipment statuses used in oneLab are used in a similar way as done in FAB300. A more extensive description of the meaning of different tool statuses is available in procedure L3_BEL_FABLAB_015.